Stainless pipes and tubes production
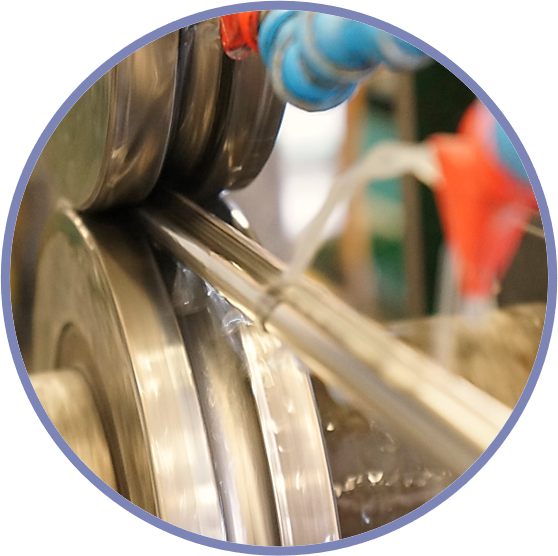
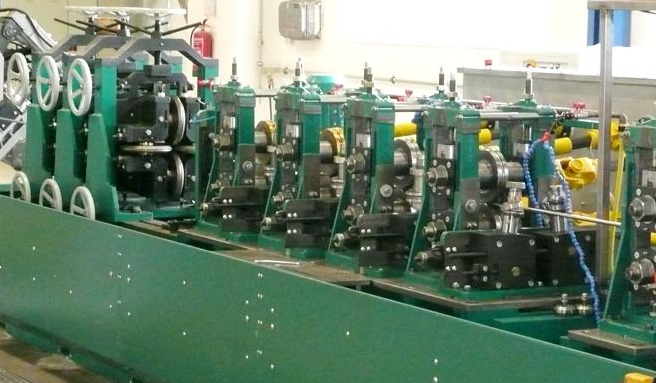

Production technology:
Longitudinal laser welding under protective atmosphere. The automatic welding line uses the latest fiber laser technology, also known as FIBER laser.
Manufactured grades:
- Austenitic
- Ferritic
- Martensitic
- Duplex (austenitic-ferritic)
Standard production dimensions:
- Pipe diameter from 8 to 66 mm
- Wall thickness from 0,8 do to 2,5 mm
- Square tubes from 10x10 mm to 50x50 mm
- Rectangular tubes from 15x10 to až 60x40 mm
- Straight lengths 6000 mm as standard or according to customer requirements, tubes can be supplied in coils with an inner diameter of 600 mm with a coil weight of around 500 kg
Production standards and technical delivery conditions
- EN 10217-7
- EN 10296-1
- EN 10296-2
- EN 10305-5
- Material certificates according to EN 10204 3.1.
Cold drawing of pipes
Production technology:
The semi-finished products are laser welded tubes. The drawing method can be broaching for tubes with a precise outer diameter or drawing on a free mandrel to calibrate the inner diameter or wall thickness.
Product characteristics:
- High dimensional accuracy (outer and inner diameter or wall thickness)
- Smooth drawn surfaces, low roughness
- Excellent mechanical properties
Production dimensions:
- Pipe diameter from 4 to 20 mm
- Wall thickness from 0,4 to 1,2 mm
- Straight lengths 6000 mm as standard or according to customer requirements
Laser and CNC cutting

Automatic CNC saw:
- Productive cutting of stainless steel materials
- Automatic tube end brushing system
- For shorter lengths, the possibility of tumbling to shrink the edge
Laser CNC machines:
- For cutting and shaping of stainless and carbon steel, aluminium, copper, brass and other non-ferrous alloys
- The advantage is high precision, very good cutting quality and stability of the production process
- 3D models in STP or IGES format can be used for programming
Automatic system for chipless cutting:
- Chipless cutting technology with high cutting precision
- Minimum material loss between cuts
- Suitable for cutting thin-walled tubes and small diameter tubes
- Suitable for applications with an emphasis on cleanliness (no chips, biological lubrication)
- Applications for heat exchangers, air conditioning, heating, cooling of solar technology, automotive fuel and brake lines
Heat treatment and brazing
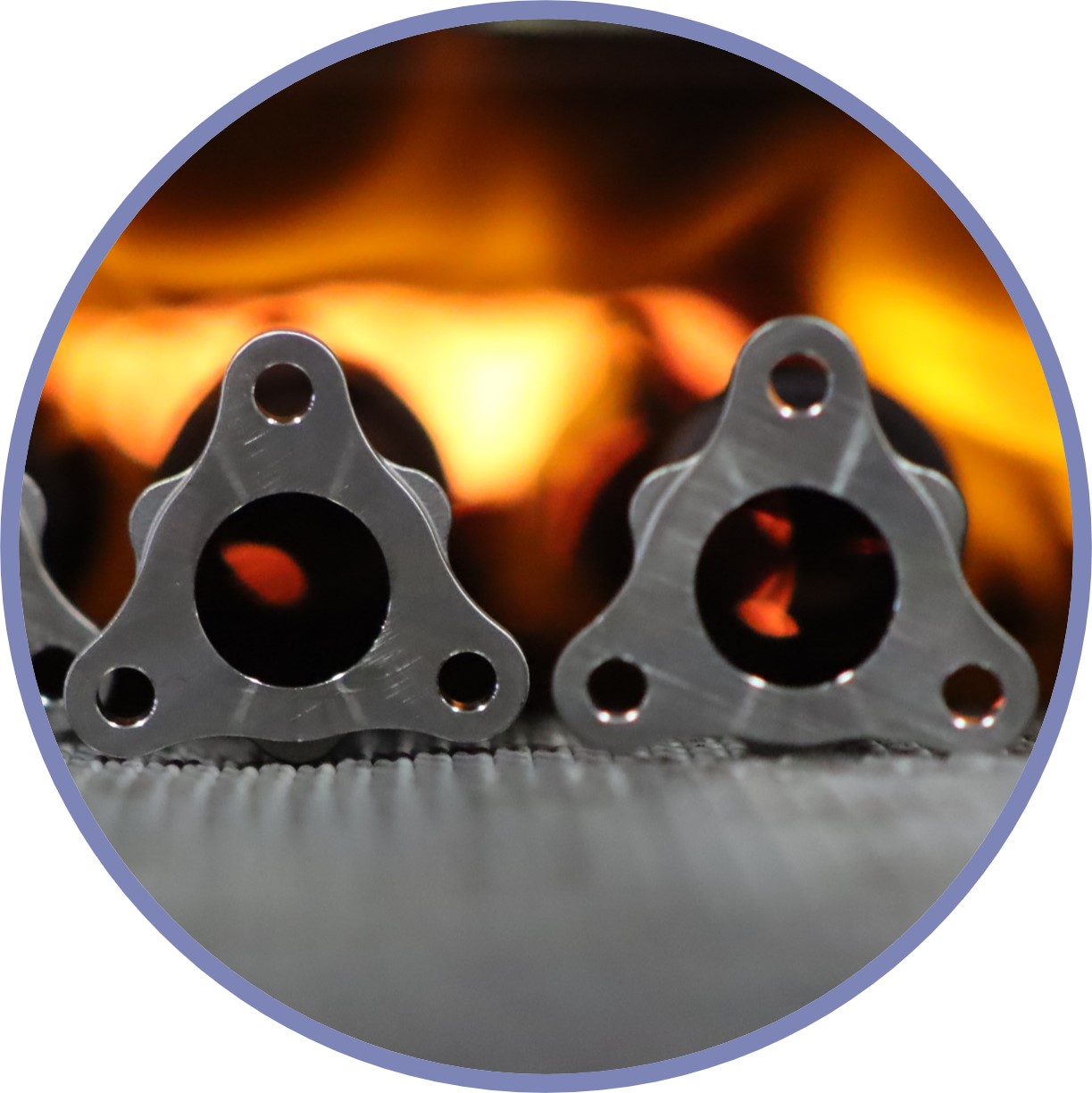
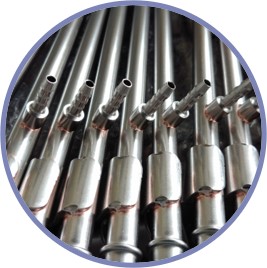
Production technology:
Continuous belt furnaces with protective atmosphere and control system for automatic control of the production process. The furnaces are fully programmable, temperature and speed parameters can be digitally archived.
Product applications:
- Stainless steel annealing to specification
- Carbon steel annealing to specification
- Heat treatment of duralumin material for the following forming processes
- Brazing using copper-based paste
- Brazing using nickel-based paste
- Soldering of supplied composites
Production specifications:
- The maximum temperature for stainless steel processing is 1120 °C, working area clearance 100 mm, belt width 300 mm
- The maximum temperature for processing carbon steel is 1150 °C, the clearance of the working area is 150 mm, the belt width is 300 mm
Grinding of pipes and tubes
Production technology:
Grinding by non-contact orbital system at reduced temperatures and pressure, the tube passes smoothly through the working area without rotation. Bended pipes and tubes can also be ground
Characteristics and specification:
- Unified surface and roughness
- Surface preparation for further processing
- Design elements of interiors
- Improvement of corrosion-resistant material properties
Production specifications:
- Pipes from 9 mm do 100 mm OD
- Tubes from 9 x 9 mm do 100 x 100 mm OD
- Standard roughness Ra 0.4 or as required
Bending
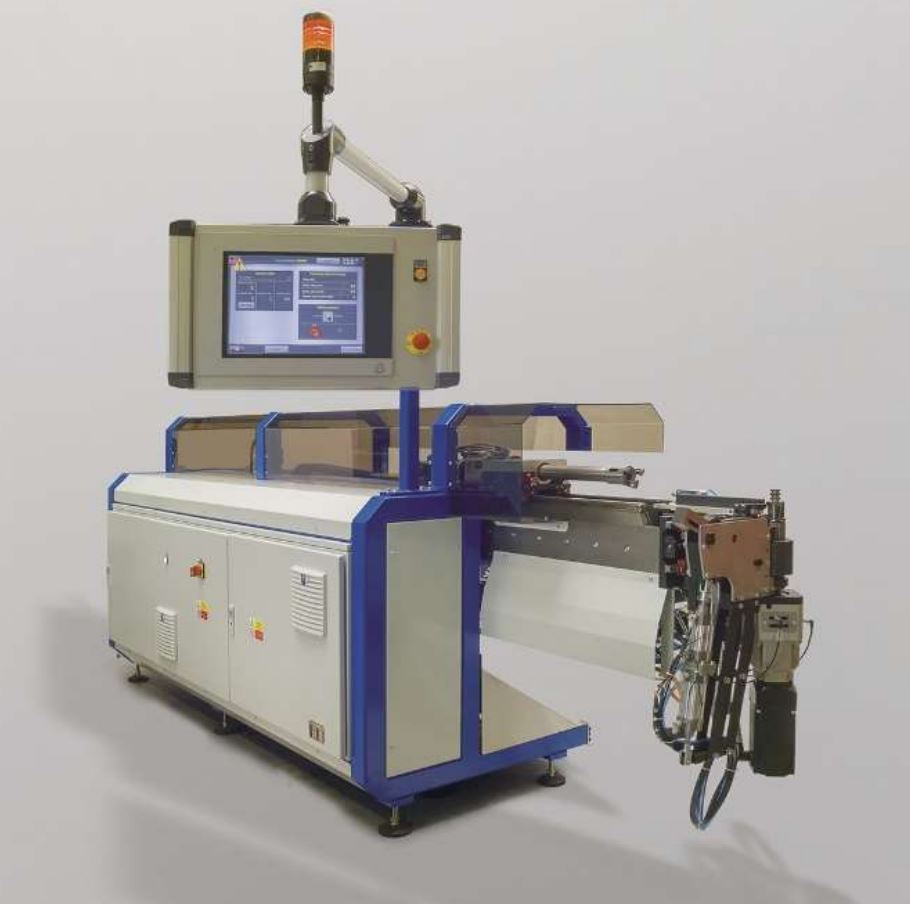
Production technology:
Precise spatial cold bending of tubes according to CAM data supplied by the customer or in our own design
Product applications:
- Automotive and energy industry
- Parts of machinery and equipment
- Industrial furniture and interior design elements
Production specifications:
- Carbon tubes from 5 mm do 12 mm OD
- Stainless tubes from 5 mm do 12 mm OD
- Aluminium tubes from 12 mm do 22 mm OD
- Length from 100 mm to 2000 mm
- Bending radius from 12 to 40 mm
Specific applications
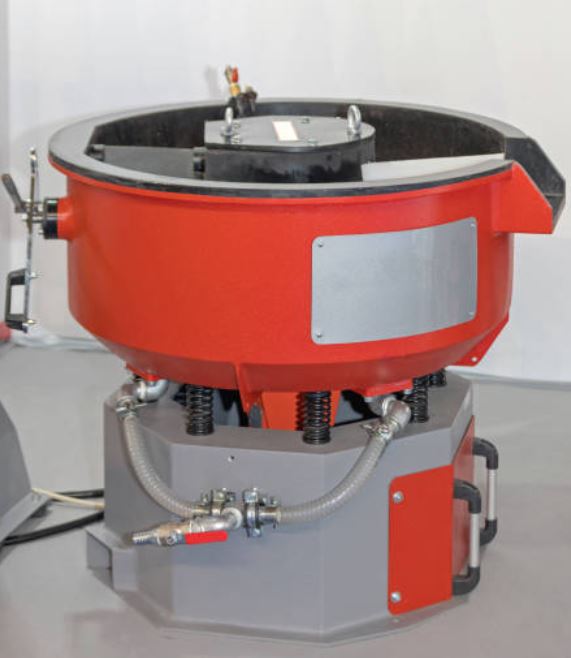
Tumbling
Polishing is a technological process in which the workpieces and the polishing agent are set in mutual motion by the rotation or vibration of the machinery. The material is removed by the friction and impact of the polishing agent on the surface of the workpiece.
In our company we use vibratory plastering equipment mostly in combination with ceramic plastering bodies of various shapes and sizes.
Uses:
- Deburring
- Edge rounding
- Surface smoothing
- Removal of unwanted scale or rust
- Degreasing and cleaning
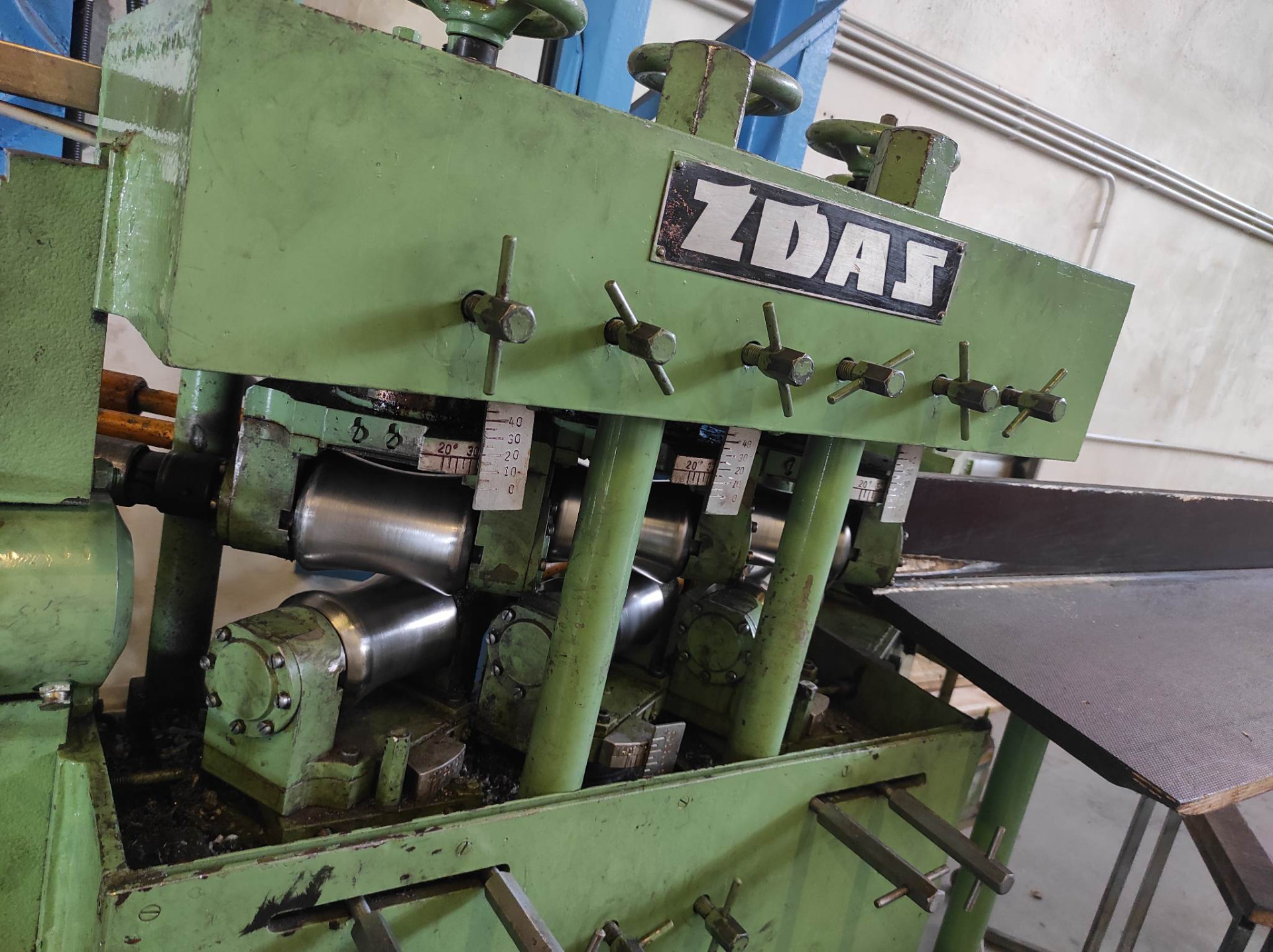
Straightening
Tube straightening is a technological forming process that changes the shape of a semi-finished product by external forces without the formation of chips.
In our company we use a straightening stool for cold forming. The tube is stretched between three pairs of mutually inclined straightening rollers, the tube is moved by the first pair of rollers, while the other two pairs balance the tube.
Uses:
- When straightness of pipes is required
- For pipe alignment after heat treatment
Tube straightening is a technological forming process that changes the shape of a semi-finished product by external forces without the formation of chips.
In our company we use a straightening stool for cold forming. The tube is stretched between three pairs of mutually inclined straightening rollers, the tube is moved by the first pair of rollers, while the other two pairs balance the tube.
Uses:
- When straightness of pipes is required
- For pipe alignment after heat treatment

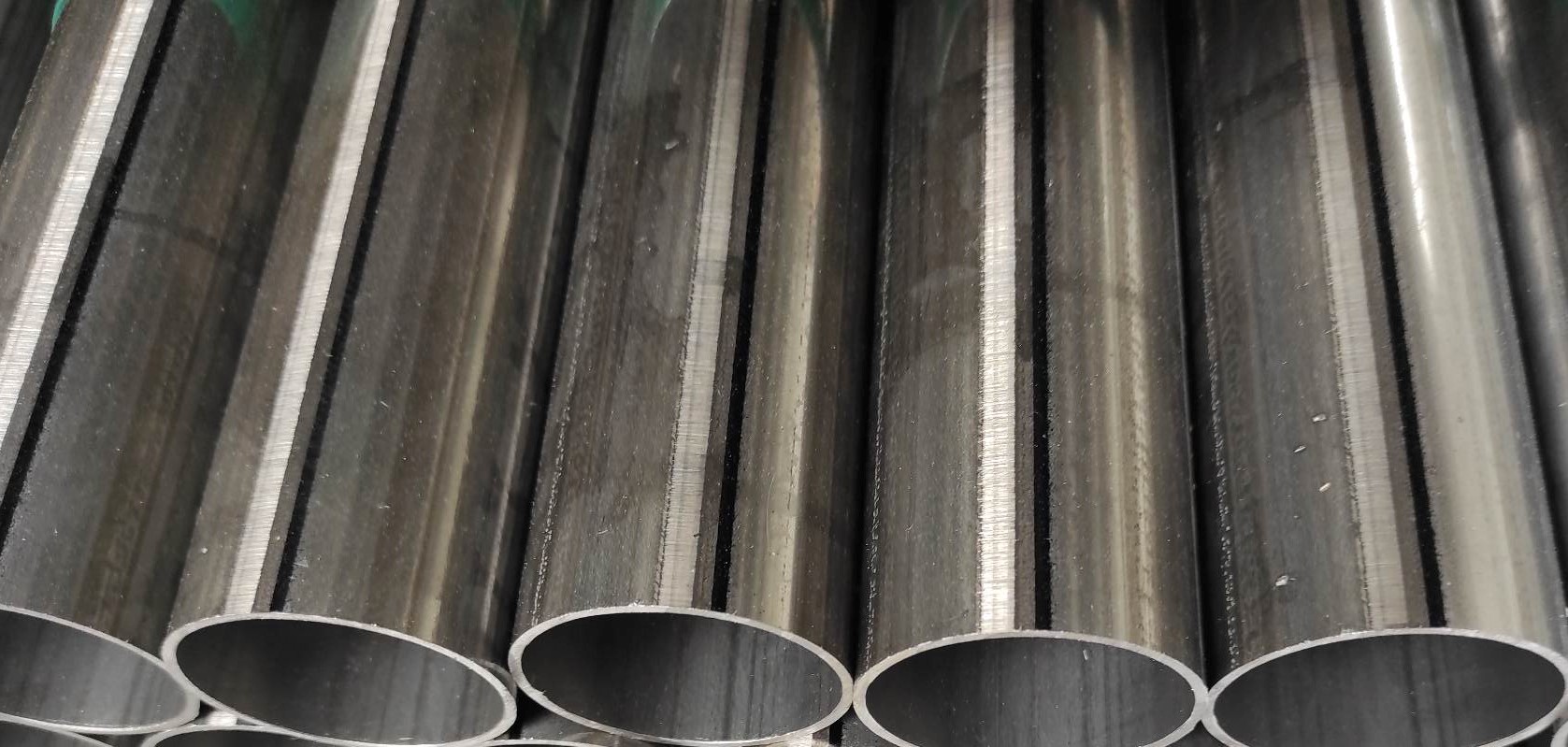
Marking and engraving
Marking and engraving is used to identify the required parameter (e.g. material quality, part number, date of manufacture, etc.) or for specific customer requirements (e.g. marking the position of the weld joint).
In our company we use the following methods for marking and engraving:
- Laser engraving (on CNC lasers during production or engraving of the final part on the engraving machine)
- Ink injection marking in continuous tube and steel production
Contact us for more information